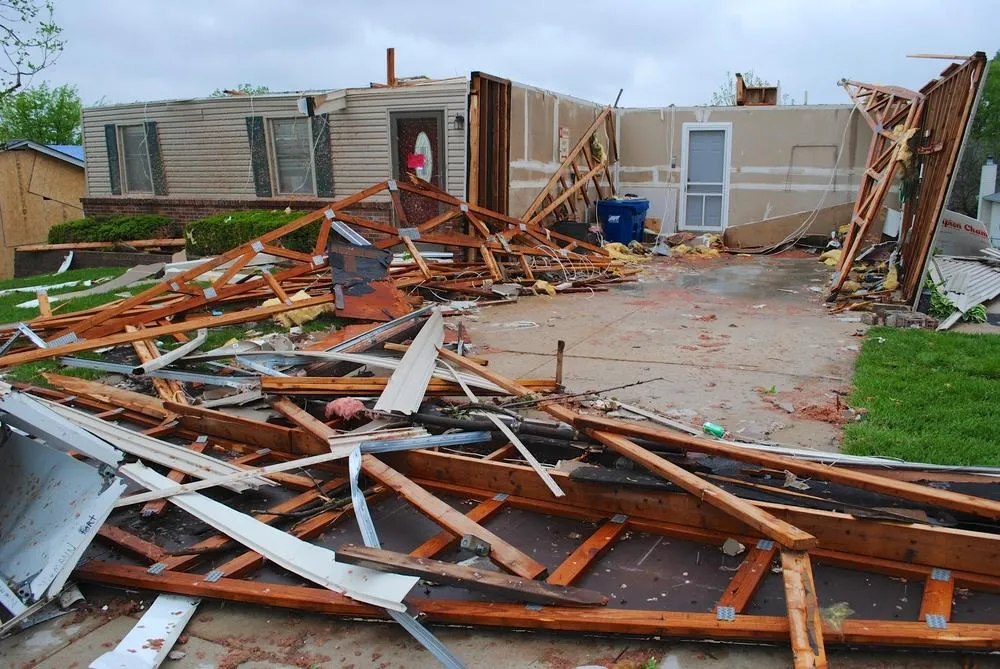
Disaster Recovery

Fast, Strong, Reliable — Using Modular Construction for Disaster Recovery
When disaster strikes, families can lose everything. Their home, their personal belongings, and their sense of safety. While the homeowner’s goal is getting their life back to “normal” as soon as possible, it is a process that just doesn’t happen as quickly as they would like. Insurance companies, local red tape, and government regulations can hinder the process of quickly replacing a destroyed or damaged home.
Overcoming the Obstacles
Americans are placing more and more demands on their homes—particularly to conserve energy, reduce environmental impact, and improve safety and security. This shift in thinking places attention on their home, rather than the sum of various components. Achieving this kind of building, known as a high-performance building, requires the deliberate consideration and integration of many attributes. In addition, the homeowner, builder, and design team need to address the planning, financing, design, and construction, as a team.
Constructing a custom home in the field makes it extremely difficult to meet the tolerances required of the building envelopment in today’s high-performance homes. The tight tolerances and inspections needed to ensure that specifications are met are a natural process in the factory environment. The challenges of the site, weather, and security are essentially eliminated by building indoors.
Is Green Building the same thing as High-Performance Building?
When it is time to rebuild, modular construction can be the solution to solve multiple issues in disaster areas. When the recovery starts, typical frustrations homeowners face include:
Lack of contractor availability
Limited amount of contractors
Price inflation of materials from local suppliers
Increased costs for required labor
Inspection delays
And the list goes on…
Modular construction minimizes the dependence on local resources by placing 85% of the home’s construction effort offsite where costs are virtually unaffected. Since most inspections are done at the factory, the strain on local inspection resources is reduced. Construction can take place simultaneously with the preparation of the site.
Peace of Mind
Modular construction is inherently stronger than site build construction. Modules must be built to be transported on a carrier to the jobsite and then lifted by a crane into position. Each module is structurally independent. Once the modules are positioned on site, they are essentially interlocked to each other by either bolts, lag screws, straps, or a combination of all of these. This makes the structure much stronger than that provided using standard conventional construction.
After Hurricane Andrew hit in 1992, the Federal Emergency Management Agency’s (FEMA) Mitigation Assessment Team conducted a study of various building types and how well they weathered the storm. In their summary the Mitigation Assessment team concluded that “in general, it was observed that masonry buildings and wood-framed modular buildings performed relatively well.” The report went on to state that “overall, relatively minimal structural damage was noted in modular housing developments. The module–to-module combination of the units appears to have provided an inherently rigid system that performed much better than conventional residential framing.”
Homes Reconstructed Using Modular Construction after Hurricane Andrew
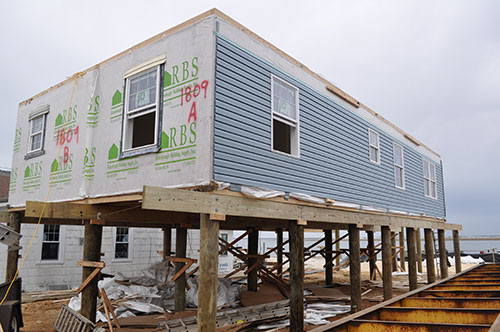
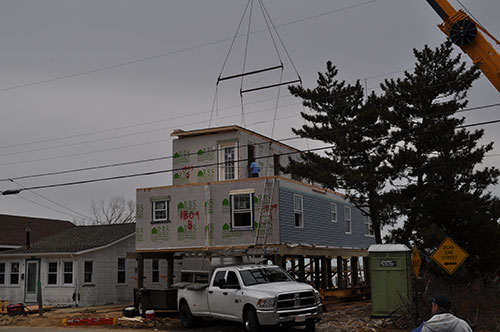